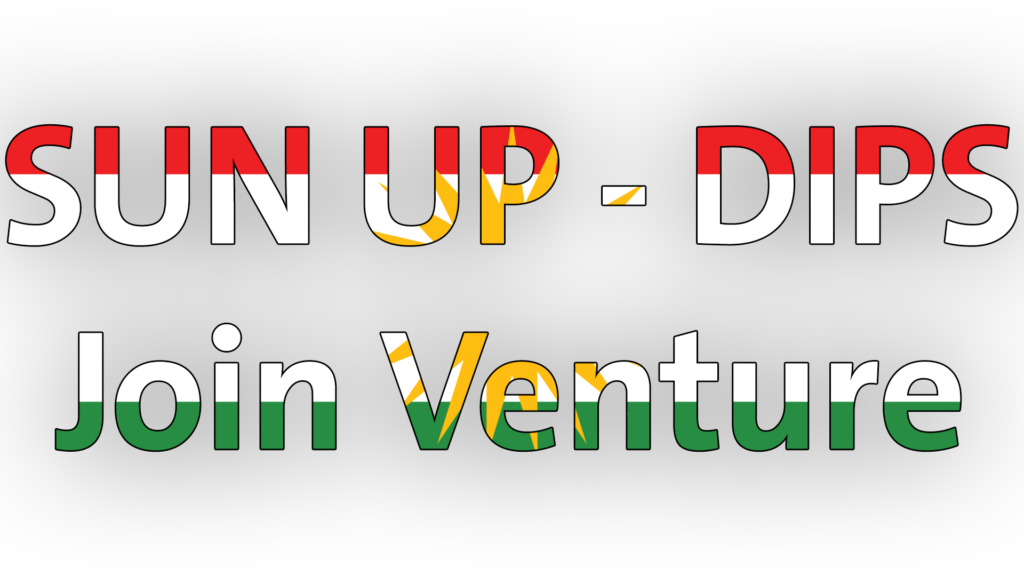
Sun Up holding - DIPS
Dips ® was established to cover the Kurdish Iraqi market requirements for NDT, Lifting Gear inspection with Rope Access Technique.
Dips ® has also added to its activities, the supply & allocation of skilled specialist manpower, through its great database of specialized and experienced manpower that has served the Oil / Gas sector.
Dips ® continues to provide value added services which reduce risk and protect customers’ investment.
Dips ® inspection services have grown with the market – providing superior support . We use the highest quality NDT methods which include UT ultrasonic, MPI magnetic particle inspection, ET eddy current, PT Dye Penetrant, Hardness Testing Services and radiographic & X-Ray .
Dips ® has the authority from Egyptian Atomic Authority to use isotope and X-Ray at radiographic activities
PEC (Pulsed Eddy Current)
Modified NDT utilize PEC-LYFT-Eddyfi equipment.
Pulsed eddy current (PEC) is an advanced electromagnetic
inspection technology used in detecting flaws and corrosion
in ferrous materials typically hidden under layers of coating,
fireproofing, or insulation. It is a screening tool.
It will detect generalized corrosion.
Pulsed Eddy Current is a unique
corrosion survey method that allows ferrous objects to be surveyed
without the need to make contact with the surface.
This means that measurements can be performed on objects
covered with insulation, asbestos, fireproofing, concrete or coating.
The high costs for removal of insulation can therefore be avoided.
Benefits:
Inspect through thick insulation and fireproofing
Save on insulation removal costs
Wall thickness up to 100mm
Lift off range up to 300mm
No problems with high temperature (tested up to 420 °c)
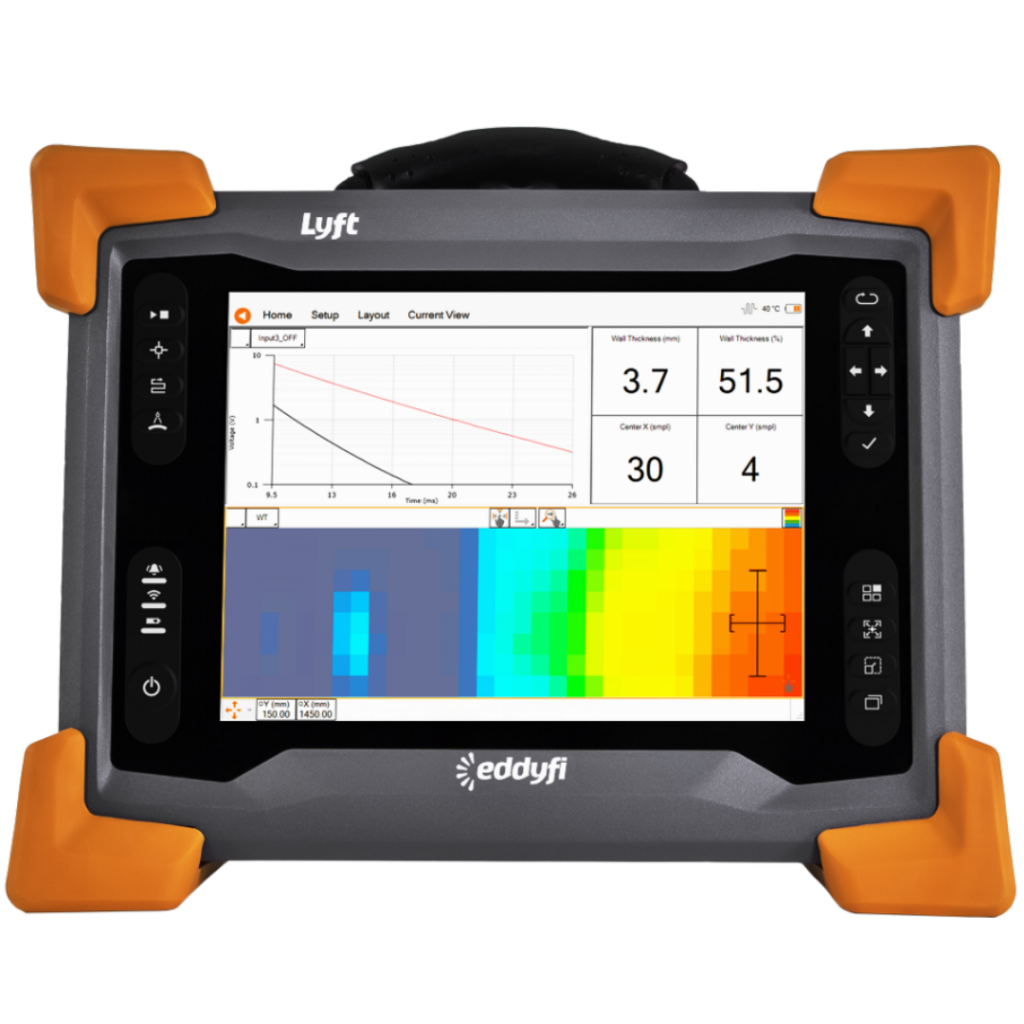
MFL Tank floor inspection (Magnetic Flux Leakage)
Modified NDT utilize MFL- Silverwing- Floormap 3Di-M- Eddyfi equipment.
It is an automated scanning system for accurate
and efficient corrosion inspections on tank floors.
By combining two technologies – Magnetic Flux Leakage (MFL)
and Surface Topology Air-Gap Reluctance Sensor (STARS)
it can detect and size corrosion and pitting
on storage tanks and pipelines.
Benefits:
Full tank floor mapping mode
Advanced defect sizing and classification tools
High probability of detection
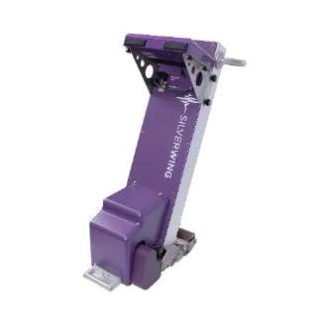
MFL Tank floor inspection (Magnetic Flux Leakage)
Modified NDT utilize MFL- Silverwing- Floormap 3Di-M- Eddyfi equipment.
It is an automated scanning system for accurate
and efficient corrosion inspections on tank floors.
By combining two technologies – Magnetic Flux Leakage (MFL)
and Surface Topology Air-Gap Reluctance Sensor (STARS)
it can detect and size corrosion and pitting
on storage tanks and pipelines.
Benefits:
Full tank floor mapping mode
Advanced defect sizing and classification tools
High probability of detection
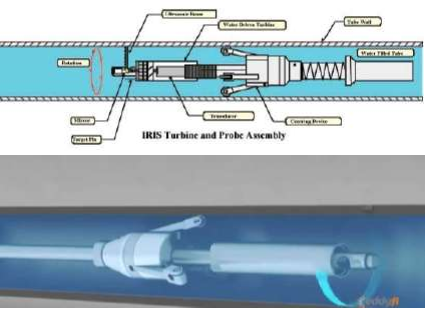
ECT Tube Inspection (Eddy Current Testing)
Modified NDT utilize Ectane 2- Eddyfi equipment for ECT Tube Inspection. Eddy current testing is an electromagnetic non-destructive testing technique used to inspect non-ferromagnetic materials. It is widely used to examine tubing in heat exchangers, steam generators, condensers, air coolers and feed water heaters. This technique is used for detection and sizing of cracks, corrosion, erosion, and mechanical damage. EC is a very fast inspection method.
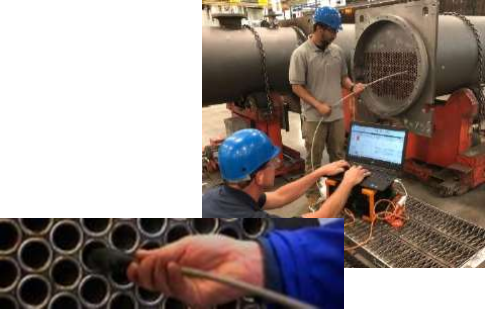
MFL Tube Inspection (Magnetic Flux Leakage)
Modified NDT utilize Ectane 2- Eddyfi equipment for MFL Tube Inspection. Magnetic flux leakage (MFL) is an electromagnetic non-destructive testing technique used to detect corrosion and pitting in ferromagnetic materials. MFL uses a powerful magnet to magnetize the conductive material under test. Where there are defects (corrosion or material loss), the magnetic field “leaks” from the conductive material. It is a fast inspection technique that is effective for aluminum-finned carbon steel tubes, because the magnetic field is almost completely unaffected by the presence of such fins.
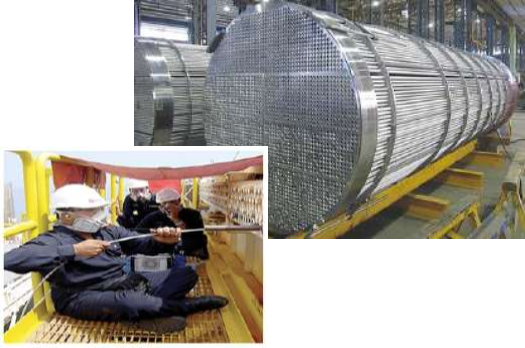
NFT Tube Inspection (Near Field Testing)
Modified NDT utilize Ectane 2- Eddyfi equipment for NFT Tube Inspection. Near-field testing (NFT) is an electromagnetic technique used to inspect tubes. It is specifically suited to detecting corrosion, erosion, and pitting in ferromagnetic materials. NFT is perfect for fin-fan tube heat exchangers because eddy currents do not go through the wall of the tube. It can detect internal defects.
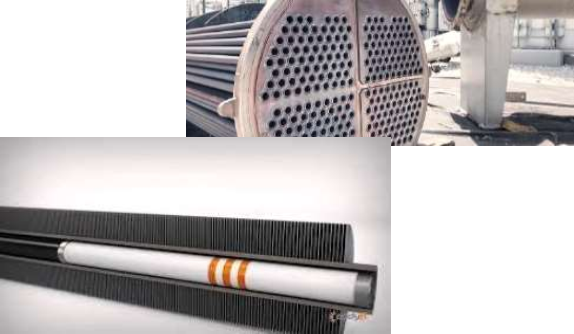
FT Tube Inspection (Remote Field Testing)
Modified NDT utilize Ectane 2- Eddyfi equipment for RFT Tube Inspection. Remote-field testing (RFT) is a non-destructive electromagnetic testing technique mainly used to find defects like corrosion and pitting in tubes. It is suitable for ferromagnetic materials. RFT can detect both internal and external defects.
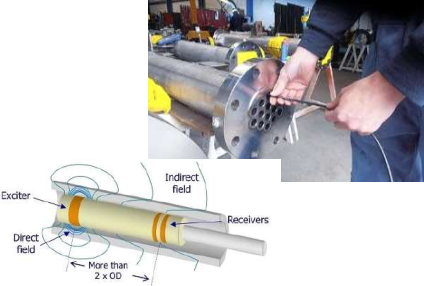
SRUT (Short Range Ultrasonic Testing)
Modified NDT utilize ISONIC 2005, OmniScan X3 and OmniScan MX2 for SRUT. Short Range Ultrasonic testing (SRUT) is a screening non-destructive test method to detect corrosion on the pipe wall or plates concealed under support structures or structural shell. The special SRUT probe is placed away from the area of interest (generally concealed surface) to scan up to 1m of material length without losing adequate sensitivity. Annular rings under the Tanks shells are best inspected using Short Range Ultrasonic testing.
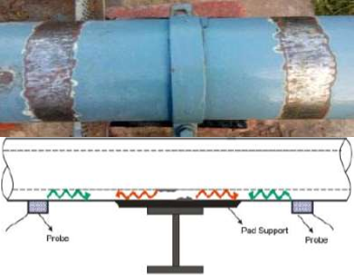
Phased Array
Modified NDT utilize OmniScan X3 and OmniScan MX2 for Phased Array inspection. Phased Array uses arrays of ultrasonic beams that are computer-controlled and steered electronically. An array is a group of transmitters and receivers, generally called array elements. This advanced ultrasonic testing method is both fast and highly efficient at defect detection due to multiple simultaneous sound beams (angles). It is used to detect discontinuities such as cracks or flaws in welds. In addition to detecting flaws in welds, phased array is also used for corrosion mapping.
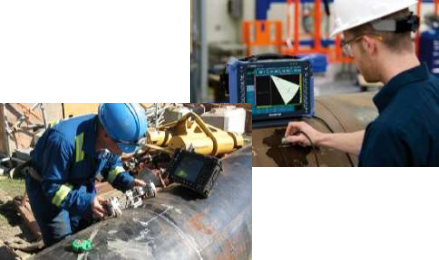
TOFD (Time of Flight Diffraction)
Modified NDT utilize OmniScan X3 and OmniScan MX2 for TOFD inspection. Time-of-flight-diffraction is a widely used advanced ultrasonic testing method to detect cracks or flaws and size them in welds. It can detect planar defects and cracks not perpendicular to the measured surface. The defect height can also be exactly determined and the high probability of detection (POD) associated with this method greatly improves risk reduction and calculation accuracy.
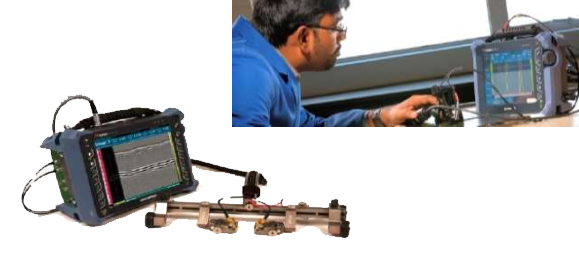
Digital Radiography
Modified NDT utilize Duerr scanner for Digital Radiography. Digital radiography is an advanced technology based on digital detector systems instead of films, in which the image is displayed directly on a computer screen without the need for developing chemicals or intermediate scanning. Advantages of advanced digital radiography over conventional radiography is that exposure time can be shorter, no chemical evaluation is needed, better-quality testing and higher contrast image as compared to conventional radiography.
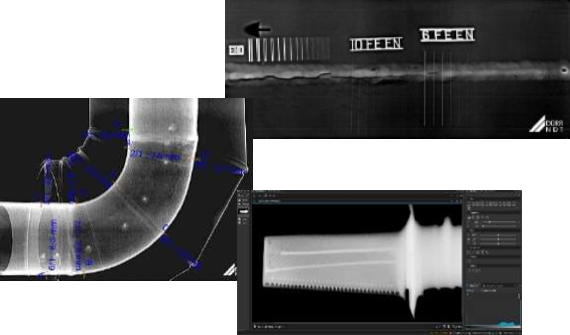
Acoustic Emission
Acoustic emission testing is a non-destructive testing (NDT) technique that detectsand monitors the release of ultrasonic stress waves from localized sources when a material deforms under stress. Acoustic Emission can be conducted during operation. This technique is used to detect a range of damage mechanisms including, but not limited to, fiber breakages, friction, impacts, cracking, delamination and corrosion in their early stages, before they become significant issues. Acoustic emission is used for assessing structural integrity and for health monitoring of components
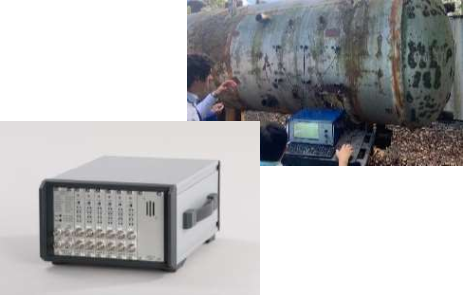
Indirect Visual Testing
Modified NDT utilize End Scope yateks Model p680fm for indirect visual testing. Modified NDT performs indirect visual testing of materials with specific cameras and video endoscopes in places that are difficult or impossible to access by humans. Endoscopes allow for an internal inspection without disassembly, saving time and money. With advanced visual testing it is easier to follow defect development and product state.
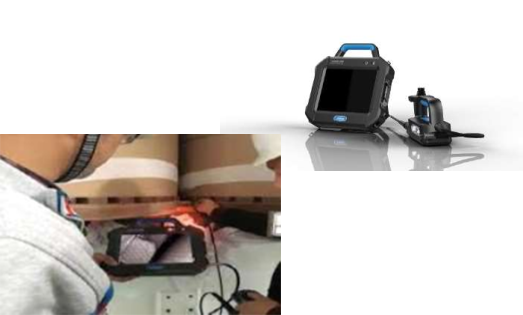
Indirect Visual Testing
Modified NDT utilize End Scope yateks Model p680fm for indirect visual testing. Modified NDT performs indirect visual testing of materials with specific cameras and video endoscopes in places that are difficult or impossible to access by humans. Endoscopes allow for an internal inspection without disassembly, saving time and money. With advanced visual testing it is easier to follow defect development and product state.
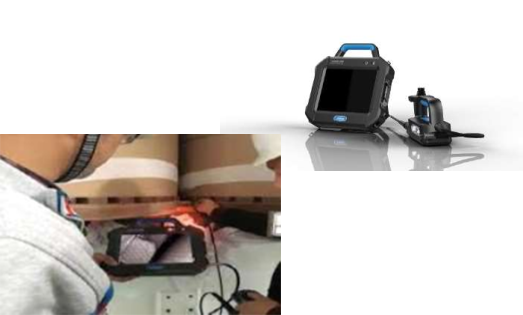
Ultrasonic Testing
Conventional Ultrasonic Testing (UT) inspection is a commonly-used non-destructive testing (NDT) technique that measures the propagation of mechanical vibrations (ultrasonic waves) through a material to examine properties, measure thickness and detect a range of discontinuities, including corrosion/erosion, flaws and cracks. It is used to detect surface and sub-surface defects and supply accurate readings regarding discontinuity size and shape.
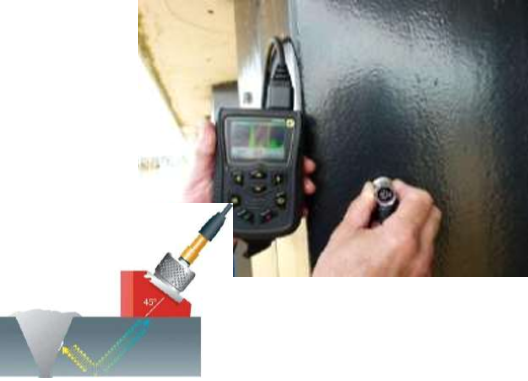
Radiographic Testing
Radiographic Testing (RT) inspections use X-Ray or Gamma ray (Ir-192, Co-60) sources to view and assess the internal structure of an asset. RT is sensitive to corrosion, changes in thickness, voids, cracks, and material density changes, and is able to detect both surface and sub-surface defects with minimum surface preparation required. Radiographic Testing (RT) accurately locate, size, and identify the defects. It provides a permanent record of the inspection.
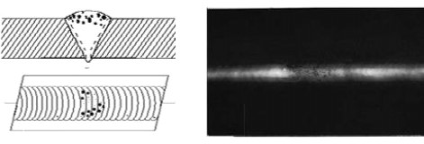
Magnetic Particle Testing
Magnetic Particle Testing is a quick, cost-effective NDT inspection method to detect surface and near-surface discontinuities. In MT, the ferromagnetic material is magnetized and finely-milled iron particles coated with a dye pigment is applied. The particles indicate a discontinuity in the material by clustering directly over it, which can be visually detected under proper lighting conditions. Thickness measurement
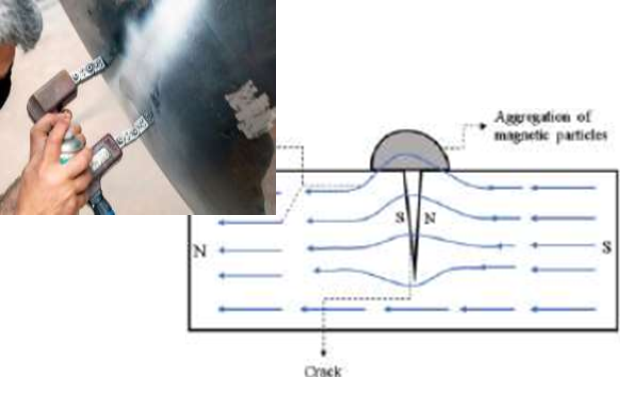
Penetrant Testing
Penetrant Testing (PT) is a non-destructive method used for finding surface-breaking discontinuities on relatively smooth, nonporous surfaces. It is a low-cost technique and can inspect complex geometries easily. In PT, assets do not have to be disassembled or removed from the facility for inspection, making the inspection process quick and efficient
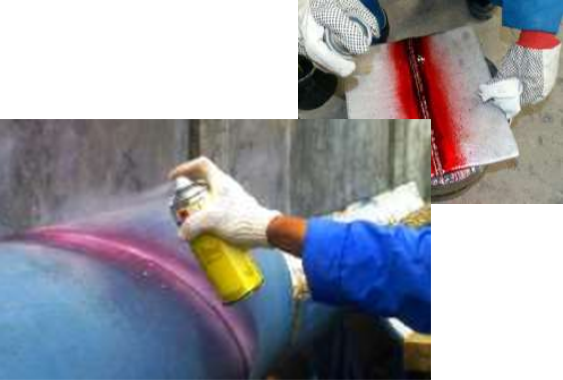
Visual Testing
Visual Testing (VT) is a basic and cost-effective method of inspection and is used to gain a quick indication of the inspected specimen or asset. It is the process of looking over a piece of equipment using the naked eye to verify the general integrity. Visual testing can be performed in direct mode (with the bare eye) or via an indirect method, by mirrors, cameras and other equipment also called advanced visual testing.
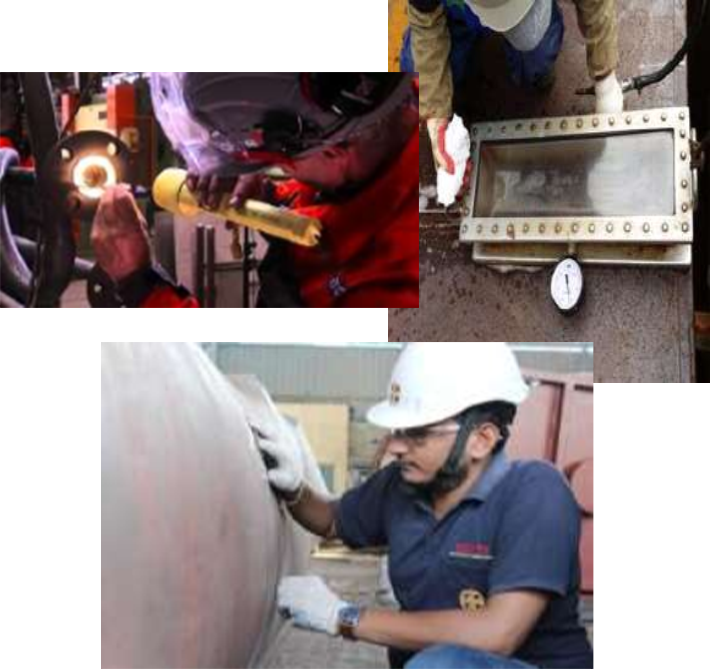
Vacuum Box Testing
Vacuum box testing is a non-destructive testing (NDT) method used for locating welding leaks. A vacuum box and a compressor create a high or low-pressure vacuum and a detergent solution is applied to the test area. The detergent bubbles help to identify the leaks within the created pressure envelope (formation of bubbles as leakage gas passes through the solution). The main objective of the Vacuum box testing technique is to locate leaks in welds due to through-thickness discontinuities.
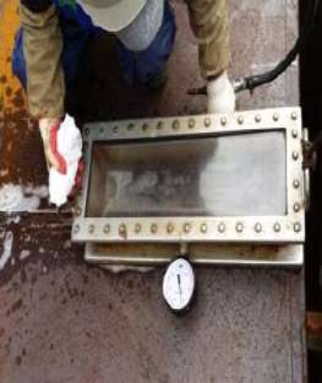
Hardness Testing
Hardness is the measure of how resistant a material is too various kinds of permanent shape deformation when a force is applied. Hardness testing makes it possible to determine material characteristics such as strength, ductility and wear resistance. It also shows whether the heat treatment process has been carried out properly. These properties can be critical for the intended application of a material.
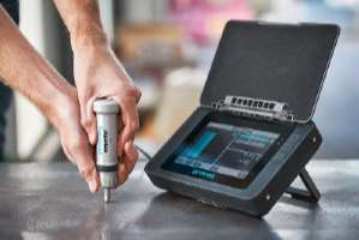
Positive Material Identification (PMI)
Positive Material Identification is a specialized non-destructive testing method for identifying the composition of components and material. PMI provides information of the grade of metal and on the alloy composition. The mechanical integrity of safety critical plant is dependent on the correct materials being used for vessels, piping, valves and pumps. If the incorrect material is used, the design assumptions are invalid and the components may fail due to the material having lower strength or poor corrosion resistance
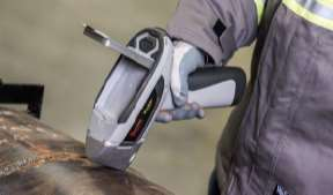
Holiday Test
Holiday test is an inspection method used to detect discontinuities such as pinholes and voids in painted/coated surfaces using specialized tools and equipment. Holidays tests work on the concept of electrical conductivity. Metal substrates are excellent conductors of electricity, and therefore allow current to flow through them. On the other hand, many coatings are poor conductors of electricity and resist the flow of electricity. Using this principle, holiday tests use instruments to locate flaws in anticorrosive paints and coatings.
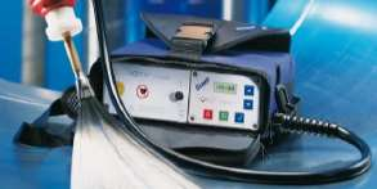
Online PSV testing calibration
Modified NDT utilize Online PSV testing calibration- AccuTest equipment.
The old way of PSV/PRV testing could be summarized in one word: downtime.
First, the plant went down, then valves were disassembled, and finally,
the valves were transported offsite for testing. This way was time-consuming,
costly and high risk. But using the AccuTEST System, PSV/PRV testing comes to you,
right where the valves actually operate, without adjustment in operating
pressure which is time saver, cheaper and Lower risk.
Benefits:
Reduces downtime. No need to place the plant off-line for a week
and remove the valves, or sending them to an outside testing facility.
Reduces loss of revenue by preventing the risk of safety valve damage during transportation for testing.
No system discharge (No fuel costs, so improves the environmental conditions)
No dismantling of the safety valves from the system (saves time and money)
For welded valves no cost for cutting and subsequent welding inspections
No need for shutdown to calibrate and test PSV.
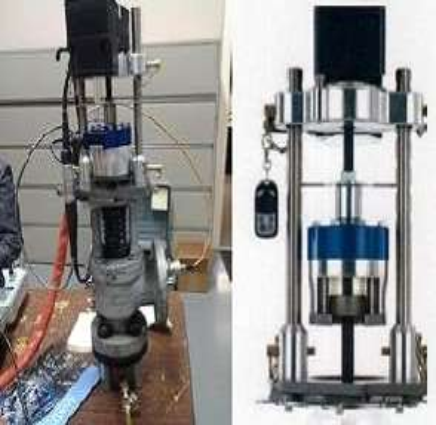
PWHT (Post Weld Heat Treatment)
Modified NDT has 9 PWHT machines of 70 KVA Power units and 65 KVA Power Units. A post weld heat treatment is a process that involves elevating the temperature of a material or materials following a welding process. A post weld heat treatment is performed to alleviate residual stresses, increase the strength, increase or decrease the hardness, and reduce the risk of cracking. An array of heating processes can be used to carry out post weld heat treatment.
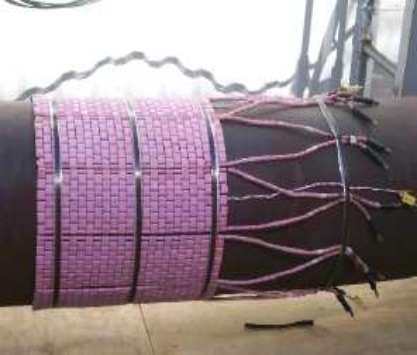
Lifting Equipment Inspection
DIPS has full LEEA Membership (Lifting Equipment Engineers Association) and is specializing in thorough examination & testing of the lifting equipment to ensure that it is fit for use in accordance with British Standard or other International Standard. Our specialist team are highly trained in the field of all types of lifting accessories and equipment inspection ensuring to meet the minimum safety requirements. Send a detailed report stating deficiencies for inspected equipment that is deemed unsafe. When deficiencies are corrected or repairs are completed , proper tests and certificates will be issued. The examination can range from visual inspection, NDT inspection, functional testing, or load testing. Once the item has passed the test, a “Report of Thorough Examination” is issued.
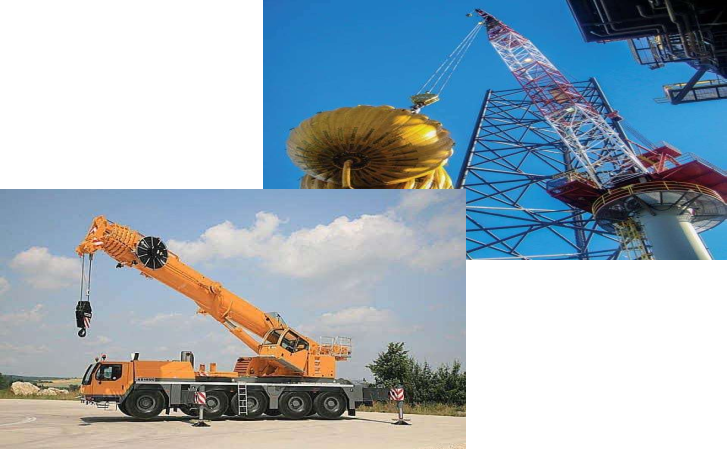